行业新闻
汽车白车身焊接质量控制措施研究
2018年09月19日
随着我国汽车工业的快速发展,其生产工艺复杂,质量控制涉及到冲模结构的构思、零部件公差的正确选取、冲压工艺分析、焊接夹具机构的构思、合理分配、焊接工艺分析及冲压件检具的使用等方面内容。其中以白车身焊接工艺分析最为关键,是为操控者人身安全与车身整体强度的保障。
一、焊接工艺分析
电阻点焊对两金属件间原子的结合,是通过电流对金属件产生的电阻热融化来实现。为确保焊接变形较小及稳定,焊接过程中对焊点间距、位置、顺序以及数量需按照焊接工艺严格操作,其各工艺参数对焊接质量的影响见下表1。
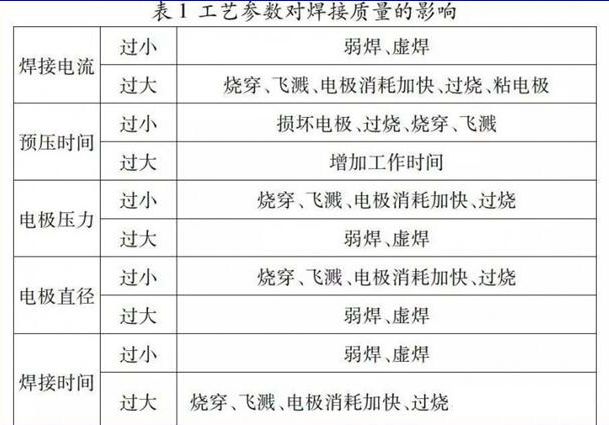
二、焊接装配件对电阻点焊质量影响
车身覆盖件装配过程中,其常见缺陷为位置错移和间隙过大,且均会导致焊后发生变形。对于一般装配件而言,其装配间隙应控制在0.6~0.8mm之间;当为小尺寸装配件且拥有较大刚度时,其间隙应控制在0.1~0.2mm之间。对于被焊件间间隙过大问题的控制,其配合间隙的消除须及时处理部件弧度上的半径不符合或折边不垂直现象。
三、焊接分流对电阻点焊质量影响
分流电流(简称分流)是指点焊过程中不经过焊接区而未参加形成焊点的部分电流。
1.影响因素
(1)点距与材料。导电性好的材料必须增大焊接点距,以此可以减小分流电流对焊接质量的影响,如铝合金比低碳钢点距大10%
(2)焊件层数。焊件层数越多,并联后分路电阻越小,同时由于各层间接触点的增多,致使电流随之增加
(3)焊件厚度。由于电流随着分路电阻的减小而增加,因此焊件越厚,则焊接点距越大
2.质量控制
(1)对关键性焊点实施定期非破坏性试验,控制频次为1次/20臺车
(2)对于电极端头面直径每周测量检验一次,记录测量结果
(3)以每周一次的频率定期测量电极压力、焊接周波及焊钳电流参数
四、焊接质量检验
1.焊点强度
焊后质量检验分为非破坏性检验与破坏性检验两种形式,其中非破坏性检验以榔头和扁铲为常用工具,主要用于生产线各工位对可錾焊点质量的检验,是为白车身焊点日常检测的一种形式,能够及时发现简单质量缺陷并采取解决措施,如弱焊与虚焊等质量缺陷,其检测频率一般为5次/班,且首次检测必须在开班正式生产前实施,并保存检测试片。破坏性检验是对焊点实施破坏检测的方式,主要工具为榔头、錾子、液压扩张钳与气动飞铲等,是为整个白车身焊点的全面、逐一检查,对于所有不合格焊点均可发现,其缺点在于车身经检测后只能做报废处理,且抽样频率较低,对于问题的及时发现与处理存在一定阻碍作用。
目前对焊点强度的检测正向无损检测方式发展,无损检测就是在不损害或不影响被检测对象使用性能的前提下,通过射线、超声波、红外线和电磁等物理方法对焊接质量进行检测的方法。其原理主要是通过利用物质的声、光、电和磁场效应,对被检测对象中是否存在缺陷进行判断,同时还能对缺陷的大小、位置等信息进行采集。由于无损检测具有非破坏性,操作方便、快捷等优点,已被广泛应用到生产实际中。
2.焊点外观
焊点外观缺陷主要有:焊点扭曲、焊点压痕过深、烧穿、未焊透以及毛刺飞溅等。根据焊点在车身所处的区域确定焊点外观质量等级。整车焊点外观等级分为3级,每级允许存在的焊点外观缺陷的数量和严重程度有所差别。
根据对焊点强度检测和外观质量的检查,可以计算出被检车身焊点的质量水平值(NQST)。以此可以衡量和控制车身焊点强度质量。NQST(焊点质量水平)值=缺陷焊点数/总焊点数x100%。NQST完成后,应及时组织相关部门召开NQST分析会,将焊点的缺陷问题进行分类并划分责任部门,各责任部门按照PDCA模式对问题进行整改以及实施验证。通过对产品质量的改进和整改措施的执行,会不断降低NQST的值,提升车身焊点综合质量。
五、结语
基于以上论述,汽车白车身焊接质量控制措施的研究是为一项精细而复杂的任务,本文通过技术分析,针对性的论述电阻点焊焊接质量的影响因素与控制措施,为我国汽车工业的可持续发展提供技术保障。然而如何全面实现我国汽车高质量生产与安全运行,使其更好的服务于人民生活与社会发展,是为一个值得我们深思的问题。
内容来自网络
AMTS 2019 第十五届上海国际汽车制造技术与装备及材料展览会将于2019年7月3-6日在上海举行,将汇聚来自中国/亚洲的知名汽车制造商和一级供应商的工程技术人员和决策者到场参观,预计将有来自世界各地800家展商参展,吸引80,000专业观众到场参观。
点击此处,申请2019展位
获取更多展会信息:
邮箱:info@for-expo.com
电话:86-21-6468 1300/6468 1550
一、焊接工艺分析
电阻点焊对两金属件间原子的结合,是通过电流对金属件产生的电阻热融化来实现。为确保焊接变形较小及稳定,焊接过程中对焊点间距、位置、顺序以及数量需按照焊接工艺严格操作,其各工艺参数对焊接质量的影响见下表1。
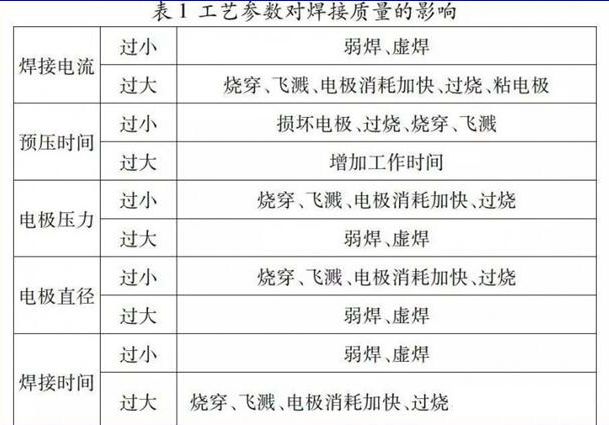
二、焊接装配件对电阻点焊质量影响
车身覆盖件装配过程中,其常见缺陷为位置错移和间隙过大,且均会导致焊后发生变形。对于一般装配件而言,其装配间隙应控制在0.6~0.8mm之间;当为小尺寸装配件且拥有较大刚度时,其间隙应控制在0.1~0.2mm之间。对于被焊件间间隙过大问题的控制,其配合间隙的消除须及时处理部件弧度上的半径不符合或折边不垂直现象。
三、焊接分流对电阻点焊质量影响
分流电流(简称分流)是指点焊过程中不经过焊接区而未参加形成焊点的部分电流。
1.影响因素
(1)点距与材料。导电性好的材料必须增大焊接点距,以此可以减小分流电流对焊接质量的影响,如铝合金比低碳钢点距大10%
(2)焊件层数。焊件层数越多,并联后分路电阻越小,同时由于各层间接触点的增多,致使电流随之增加
(3)焊件厚度。由于电流随着分路电阻的减小而增加,因此焊件越厚,则焊接点距越大
2.质量控制
(1)对关键性焊点实施定期非破坏性试验,控制频次为1次/20臺车
(2)对于电极端头面直径每周测量检验一次,记录测量结果
(3)以每周一次的频率定期测量电极压力、焊接周波及焊钳电流参数
四、焊接质量检验
1.焊点强度
焊后质量检验分为非破坏性检验与破坏性检验两种形式,其中非破坏性检验以榔头和扁铲为常用工具,主要用于生产线各工位对可錾焊点质量的检验,是为白车身焊点日常检测的一种形式,能够及时发现简单质量缺陷并采取解决措施,如弱焊与虚焊等质量缺陷,其检测频率一般为5次/班,且首次检测必须在开班正式生产前实施,并保存检测试片。破坏性检验是对焊点实施破坏检测的方式,主要工具为榔头、錾子、液压扩张钳与气动飞铲等,是为整个白车身焊点的全面、逐一检查,对于所有不合格焊点均可发现,其缺点在于车身经检测后只能做报废处理,且抽样频率较低,对于问题的及时发现与处理存在一定阻碍作用。
目前对焊点强度的检测正向无损检测方式发展,无损检测就是在不损害或不影响被检测对象使用性能的前提下,通过射线、超声波、红外线和电磁等物理方法对焊接质量进行检测的方法。其原理主要是通过利用物质的声、光、电和磁场效应,对被检测对象中是否存在缺陷进行判断,同时还能对缺陷的大小、位置等信息进行采集。由于无损检测具有非破坏性,操作方便、快捷等优点,已被广泛应用到生产实际中。
2.焊点外观
焊点外观缺陷主要有:焊点扭曲、焊点压痕过深、烧穿、未焊透以及毛刺飞溅等。根据焊点在车身所处的区域确定焊点外观质量等级。整车焊点外观等级分为3级,每级允许存在的焊点外观缺陷的数量和严重程度有所差别。
根据对焊点强度检测和外观质量的检查,可以计算出被检车身焊点的质量水平值(NQST)。以此可以衡量和控制车身焊点强度质量。NQST(焊点质量水平)值=缺陷焊点数/总焊点数x100%。NQST完成后,应及时组织相关部门召开NQST分析会,将焊点的缺陷问题进行分类并划分责任部门,各责任部门按照PDCA模式对问题进行整改以及实施验证。通过对产品质量的改进和整改措施的执行,会不断降低NQST的值,提升车身焊点综合质量。
五、结语
基于以上论述,汽车白车身焊接质量控制措施的研究是为一项精细而复杂的任务,本文通过技术分析,针对性的论述电阻点焊焊接质量的影响因素与控制措施,为我国汽车工业的可持续发展提供技术保障。然而如何全面实现我国汽车高质量生产与安全运行,使其更好的服务于人民生活与社会发展,是为一个值得我们深思的问题。
内容来自网络
AMTS 2019 第十五届上海国际汽车制造技术与装备及材料展览会将于2019年7月3-6日在上海举行,将汇聚来自中国/亚洲的知名汽车制造商和一级供应商的工程技术人员和决策者到场参观,预计将有来自世界各地800家展商参展,吸引80,000专业观众到场参观。
点击此处,申请2019展位
获取更多展会信息:
邮箱:info@for-expo.com
电话:86-21-6468 1300/6468 1550